Nautilus Systems, Inc. products are used in a wide variety of applications. Our systems are completely modular and configurable and can be implemented in many ways to solve many problems and we are adding solutions regularly. In order to better explain the capabilities of our systems and how our customers are using these systems we have included application notes based on various categories. Please review these application notes to learn more about how our systems are used and please contact us to discuss the specifics of your application.
Precision Placement
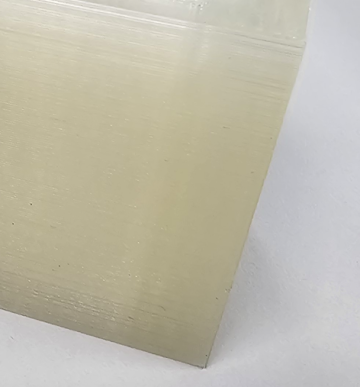
Many of our customers require our PL series of Applicators to take advantage of our industry leading placement accuracy. The PL series of applicator, based on our purpose-designed technology, provide a proven and highly reliable method for feeding, peeling, and placing adhesive-backed components in an extremely compact and highly modular system that provides maximum flexibility to the customer regarding how it is implemented and operated.
Precision placement in our systems means typical placement tolerances of +/- 0.1mm to +/- 0.35mm depending on the model of applicator chosen and the material that is running in the applicator.
See our PL Applicator Products for additional information.
Precision Placement with Printing
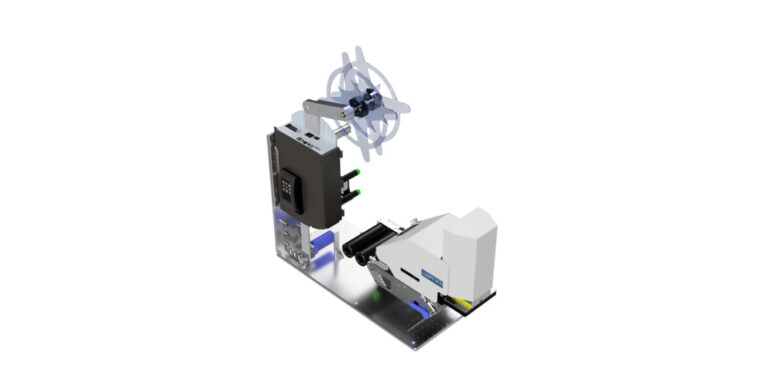
In addition to the precision placement abilities of our systems our customers frequently choose Nautilus Systems Inc products that include the ability to print on the adhesive components. In many cases those adhesive components are ‘labels’ made of typical label substrates such as paper or poly materials. Our printers provide the ability to print human readable characters, barcodes of virtually all types, and even graphics while integrated with a precision placement system.
Depending on the applicator model chosen we offer print resolutions of 300 or 600 dots per inch (dpi) with printer systems that can work with virtually all label design software packages available on the market today.
All of the applicator models with printers can be referred to as ‘print and apply’ systems. Our LC100i Applicator is a ‘print on demand’ system meaning that the label remains blank until it is to be applied and is then printed and immediately applied to a substrate.
Our PL Applicators with thermal transfer printer (-TTP) integration print into a ‘loose loop’ of material such that there is a queue of printed labels in the system at any given time. This configuration is ideal for batch or lot printing when the label to be applied does not require ‘just in time’ or ‘on demand’ printing.
See our LC100i or PL100-TTP products for additional information.
Precision Placement ‐ ‘Bubble Free’
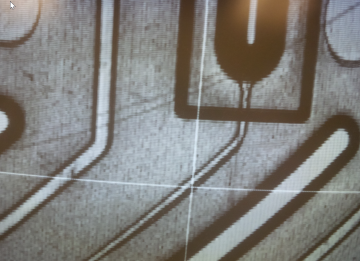
Customer requirements for precision placement can also include requirements to minimize air entrapment which is commonly referred to as a ‘bubble free’ application. Nautilus Systems, Inc has developed multiple techniques and configurations using our PL Series Applicators to obtain precision placement of adhesive components with minimal air entrapment. One of our most successful methods we refer to as Lamination Mode.
Lamination Mode takes advantage of the high performance of our applicators and our decades of experience around adhesive placement.
Some examples of applications that require lamination mode are the application of protective films to display screens for smartphones or other electronic devices and application of sealing films in microfluidic devices in which the film is used to seal fluid channels in a plastic or metal component.
There are many variables that affect the lamination process and all applications must be evaluated on a case by case basis. Please contact us for further information regarding the specifics of your application.
Precision Placement – Wrapping
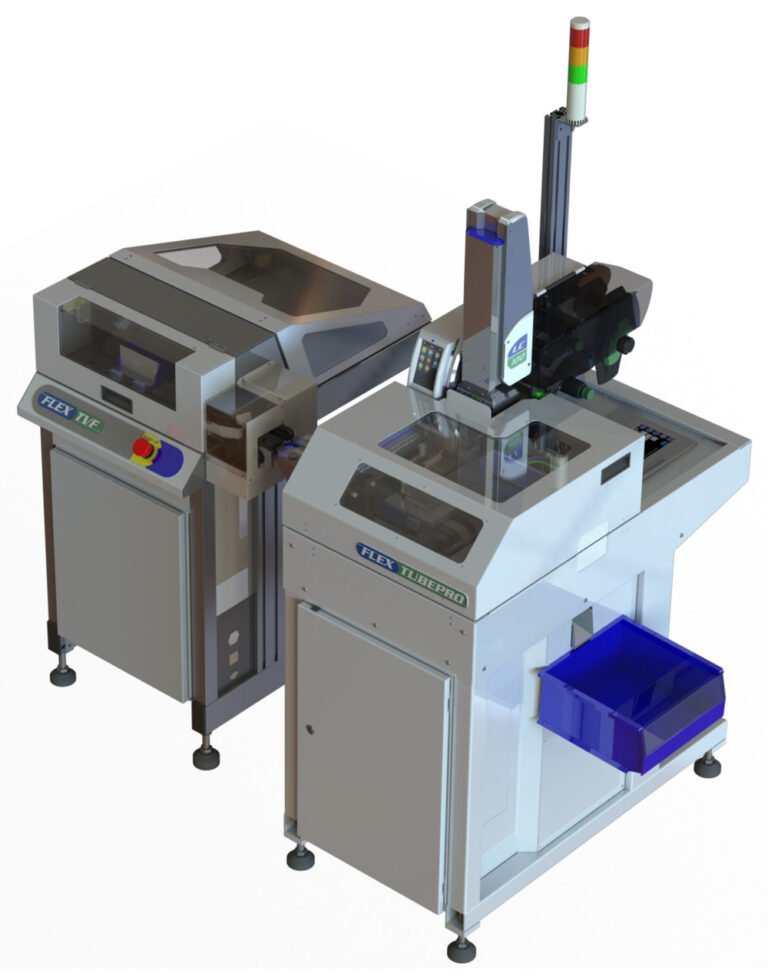
As evidenced by our Tube Pro products Nautilus Systems, Inc. has developed leading expertise for applications requiring precision placement and wrapping of die-cut parts and labels around the perimeter of substrate objects. Our Tube Pro unit is configured as a module to work with either our LC100 or PL Applicators for applying labels to Tubes, Vials, or other cylindrical shaped labware. A standard Tube Pro unit controls axial position of the label on the Tube but does not control radial position.
NSI has also developed very specialized ‘Tube Pro’ systems for wrapping labels around cylindrical and non-cylindrical devices including methods to ensure that the label or die-cut part is applied in the correct axial and radial position. These systems include hardware and software to orientate the substrate component in both of these axes. In some configurations we offer solutions that incorporate up to 8 axes of motion to ensure proper alignment and assembly of labels or other components meeting precision placement requirements in both axial and radial positions.
Please see our Tube Pro and Syringe Pro products or contact us for further information regarding the specifics of your label wrapping application.
Odd‐Shape Label or Component
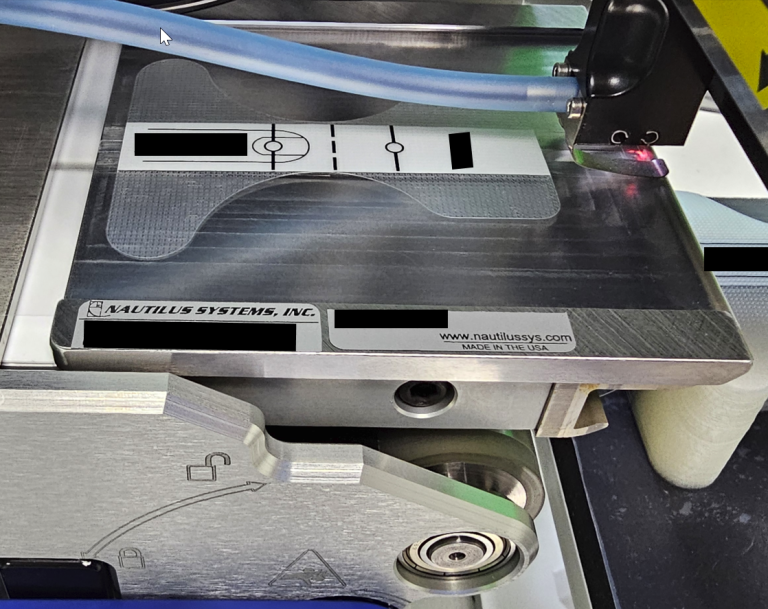
One of the major and significant benefits of our purpose-designed peel bar technology is that our applicators can accurately feed and peel adhesive-backed components regardless of their shape. We have successfully automated the placement of various parts and a wide variety of materials using or systems. Conventional ‘labeler’ equipment is best suited only to handling rectangular label shapes. Our systems are equally good for these rectangular shapes or any other shape.
A common application that takes advantage of this strength is to pick and place an array of die-cut parts simultaneously. It is possible for us to provide this function when the die-cut parts can be cut on the liner in the same array that they need to be placed onto the substrate. This can also be useful when we can pick an array of components and then apply them either ‘one by one’ or can offset or spread them to match a new pitch for application onto the substrate.
One example of this is a label of approximate size 8mm x 80mm that was to be applied to a plastic component of approximately 10 x 85mm size. Our customer was able to array the labels 5-up across a liner to match an array of 5 plastic components in an automated material handling system. Therefore, on each cycle of the applicator we placed 5 labels accurately onto the substrate components. The applicator cycle time of 2.5 seconds with 5 components assembled per cycle yielded an actual throughput of 120 label applications per minute.
In another application a customer needed to apply 3 Labels to three sides of a rectangular carton. Rather than applying the 3 Labels individually we were able to configure the Labels on the liner in anarray so that we could place all three labels at once on the sides of the carton with the carton in a flat state. In that application we were also able to implement our –TTP technology so that the three labels were printed at the same time. This virtually guaranteed that all three Labels on the carton were perfectly positioned and had the correct print data. There was no chance to mix/match labels with different data.
Please contact us for further information regarding the specifics of your application.
Two‐Sided Adhesive Assembly
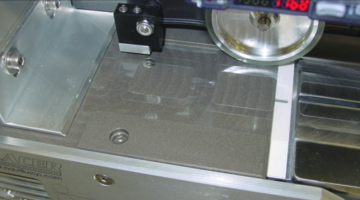
Two-sided adhesives can be known as two-sided tapes, transfer tapes, double-coated tapes, supported adhesives or by other names. Requirements to feed, peel, and place these tapes are common for Nautilus Systems, Inc. We can apply these parts using multiple techniques.
In ‘Part Apply Mode’ we can feed the exposed adhesive to a precision assembly position and then apply the substrate component to the exposed adhesive using our tamp actuator and an appropriately configured vacuum chuck. Once we have the substrate part attached to the exposed adhesive we can perform the peeling operation which removes the liner from the back side of the adhesive. At that point the die-cut part is bonded to the substrate and we can either use our tamp actuator to then apply that substrate component to another component or we can place that substrate with adhesive onto a non-stick nest from which an Operator or other automation can remove it for subsequent operations.
In other cases we can actually peel and remove the adhesive from the liner using a ‘non-stick’ vacuum chuck and apply the adhesive directly to the substrate component with no concern of the adhesive bonding the vacuum chuck itself.
Please contact us for further information regarding the specifics of your application.
Robotic Assembly
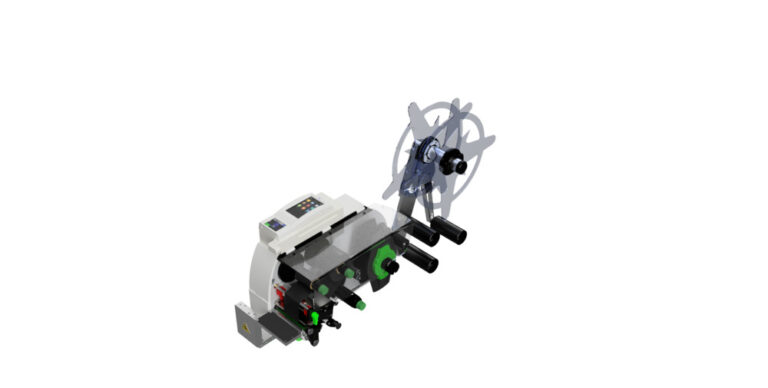
In some applications our customers require our precision feed and peel technology but prefer, for various reasons, to use their own robotic pick and place system to interface with the die-cut adhesive part. To meet that requirement we offer our ‘robot mode’ series ofproducts. Robot mode units are available for LC100, PL100, and PL165 systems.
In the robot mode configuration our systems provide their normal accurate feed and retracting peel bar technology and are configured to interface with customer robot and controls hardware.
In our PL Series of Applicators the Robot Mode units are identified with an ‘r’ in the description such as PL100r or PL165EPr. These Robot Mode units can run with labels and other adhesive components including two-sided tapes. Depending on the application requirements the customer may choose to implement a vacuum chuck on their end of arm tooling that interfaces directly with the adhesive component or they may, for two-sided tape applications, choose to capture a substrate in their vacuum chuck and have it directly contact exposed adhesive on the PL unit prior to peeling the adhesive from the liner.
The LC100r unit is a ‘print and peel’ unit and is typically used only with label or similar type materials that are compatible with thermal transfer printing. The LC100r unit prints and feeds the label to a precision pickup location from which customer robotics can capture the label and command the LC100r to peel the release liner on demand.
See our LC100r, PL100r, and PL165r products for further info.