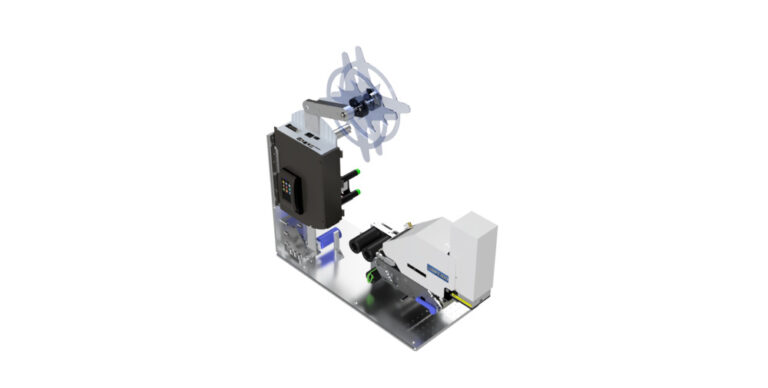
Our portfolio of ‘Print and Apply’ products incorporate our specialized technology for precision placement combined with the highest level of thermal transfer print quality available today. The LC100i Applicator is a precision system providing next label print and apply with 600 dpi printing. The PL100-TTP and PL165-TTP are systems that integrate a printer (300 or 600 dpi) with a PL series applicator. These systems include a loose loop of material and are particularly useful for precision placement requirements where ‘next label’ printing is not necessary. The Tube Pro accessory module when integrated with any of our print and apply systems provides a turn-key package for placing and wrapping labels on a variety of tubes and vials.
In addition to the precision placement abilities of our systems our customers frequently choose Nautilus Systems Inc products that include the ability to print on the adhesive components. In many cases those adhesive components are ‘labels’ made of typical label substrates such as paper or poly materials. Our printers provide the ability to print human readable characters, barcodes of virtually all types, and even graphics while integrated with a precision placement system.
Depending on the applicator model chosen we offer print resolutions of 300 or 600 dots per inch (dpi) with printer systems that can work with virtually all label design software packages available on the market today.
All of the applicator models with printers can be referred to as ‘print and apply’ systems. Our LC100i Applicator is a ‘print on demand’ system meaning that the label remains blank until it is to be applied and is then printed and immediately applied to a substrate.
Our PL Applicators with thermal transfer printer (-TTP) integration print into a ‘loose loop’ of material such that there is a queue of printed labels in the system at any given time. This configuration is ideal for batch or lot printing when the label to be applied does not require ‘just in time’ or ‘on demand’ printing. See the PL100-TTP system for additional information.
Precision Placement
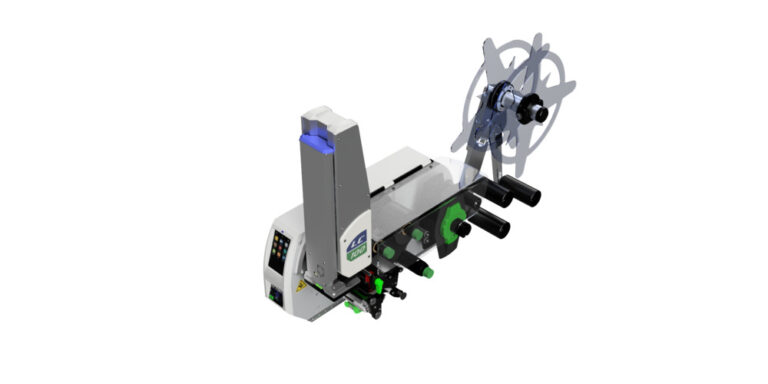
There are thousands of applications worldwide every year that require ‘print on demand’ or ‘print and apply’ applicators. Each of those applications has unique requirements that will require the automation provider to identify print and apply resources that meet those requirements. In cases that require precision placement our LC100 Applicator products are the ultimate solution. The LC100 Applicators incorporate the highest quality thermal transfer printing at 600 dots per inch (600 dpi) while ensuring placement accuracy of +/- 0.35mm in typical applications.
The LC100 Applicators incorporate purposed-designed Nautilus Systems Inc retracting peel bar technology. This technology allows us to capture the label with vacuum while it is still attached to the carrier liner or web and then remove the label from that liner. The result of this is that the label position is controlled at all times either by being attached to the liner or being captured by the vacuum chuck on our applicator.
Both the LC100i and LC100RT90 Applicators incorporate a precision tamp actuator to which we can affix vacuum chuck tooling to interface with the label material. The LC100i unit provides a vertical tamping motion and the LC100RT90 unit provides a rotating axis and a liner axis of motion which is typically used to apply labels onto a vertical plane. The LC100r Feeder is configured to ‘print and peel’ on demand from external automation and is typically interfaced with customer robotics.
See our LC100i, LC100r, and LC100RT90 Applicators and Feeders for more information.
Design Your System
Tube and Vial Labeling
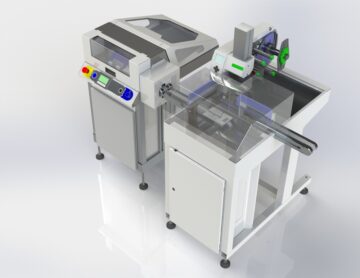
Our lab automation customers approached us with a requirement for a highly versatile print and apply labeling system for labeling of labware such as tubes, vials, cups, syringes, bottles, and more. Taking advantage of the LC100 Applicator we developed a highly modular, configurable, and versatile system for labeling these items that we named the Tube Pro module.
For each labware component that requires a label we configure a specific tool that incorporates features that locate the component axially and ensure good rotation of the component during the label application process.
The Tube Pro module can be interfaced with either LC100i Applicators or our PL100i or PL165i Applicators. The most standard configuration that we offer is the LC100 Tube Pro system which includes the LC100i Applicator and provides a precision, high resolution, print and apply on demand system with the Tube Pro module providing the motion required to wrap the label around the component.
See the Tube Pro system for additional information.
Cylindrical Device Labeling
In addition to our standard Tube Pro Module Nautilus Systems,Inc. can design and build customized ‘Tube Pro’ solutions for applying and wrapping labels on cylindrical objects or devices. In some cases we can use our standard Tube Pro methods but in larger formats to handle large parts. In other cases we can implement additional automation technology to allow us to identify features on the Object or Device and locate the Object or Device radial position relative to that feature to ensure specific radial positioning of the label or adhesive component on the Object or Device.
Please contact Nautilus Systems, Inc. for further information regarding Cylindrical Device Labeling applications.
Non‐Cylindrical Device Labeling
In cases that customers need to apply and wrap Labels or Adhesive Components on Non-Cylindrical Devices or Objects Nautilus Systems, Inc. can design and build specialized tools for the application.
Non-Cylindrical Devices cannot be labeled using the same methods as used for Cylindrical Devices. Nautilus Systems, Inc. has devised specialized methods using our PL Applicators and custom tooling to provide a highly accurate and robust solution for labeling these devices.
Please contact Nautilus Systems, Inc. for further information regarding Cylindrical Device Labeling applications.
Syringe Labeling
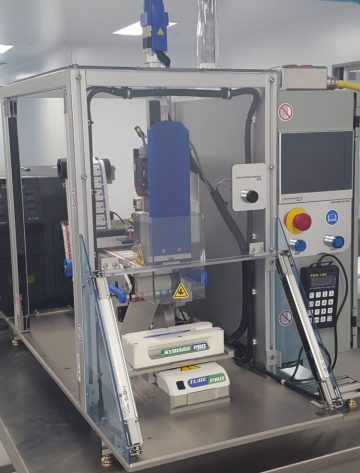
Syringe labeling is similar to tube and vial labeling but with special requirements specific to the syringes. Our Syringe Pro modular tool, combined either with one of our PL or LC series of Applicators can provide a specialized system for automatic placement of labels onto various Syringes.
See the Syringe Pro system for additional information.
Microwell Plates
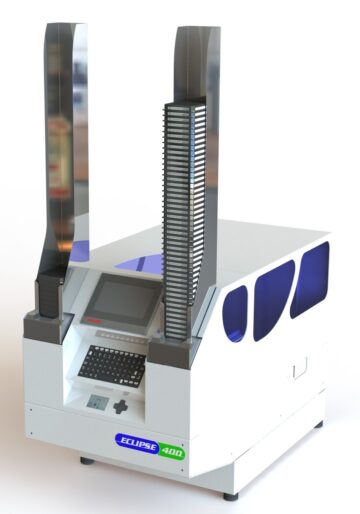
Microwell Plates, also referred to as microtiter plates, micro plates, or multiwell plates are commonly used in in analytical research and clinical diagnostic testing laboratories. There are a very high volume of these Plates used every year worldwide and typically the Plates require identification labels. In response to demand for high quality Plate Labeling Automation Nautilus Systems, Inc. has developed a series of products known as our Eclipse Plate Labeling Systems. As with all of our products we have taken a modular approach to designing these systems which allow our customers to specify the configuration that best matches their requirements at the most affordable cost level.
Our Eclipse Plate Labeling Systems are all based on our LC100RT90 Applicator. This model of Applicator is purpose- designed for Plate Labeling. It provides high resolution printing, total programmability of printed data, precision placement, and the ability to inspect the printed data prior to placing the label on the Plate. We emphasize this point because no other label application system offers this feature. We can inspect the label and ensure that it is ‘good’ prior to removing it from the liner. If a label is inspected and deemed ‘bad’ we simply leave the bad label on the liner and it will be collected in the liner waste material automatically and never applied to a Plate
Please refer to our Eclipse Plate Labeling System pages for more detailed information.
In‐Line Inspection and Auto Reject
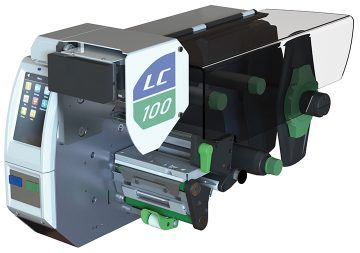
Nautilus Systems, Inc, per demand from our customers, has developed unique solutions to allow us to Inspect Labels or Die-Cut parts on the liner and then automatically handle rejected labels as integrated components of our applicators. All of this while still maintaining all of the other features and abilities of our applicator systems.
Our LC100RT90 Applicator provides high resolution printing, total programmability of printed data, precision placement, and the ability to inspect the printed data prior to placing the label on the Substrate. We emphasize this point because no other print and apply label application system offers this feature. We can inspect the label and ensure that it is ‘good’ prior to removing it from the liner. If a label is inspected and deemed ‘bad’ we simply leave the bad label on the liner and it will be collected in the liner waste material automatically and never applied to a Substrate.
In our PL Applicators we have implemented a Shuttle Chuck option that provides us the ability to inspect labels using Vision or Barcode Scanners while the label is still attached to the liner. Depending on the inspection results we can automatically peel and place Labels that Pass onto a Substrate. For Labels that Fail we can automatically handle those Labels and place them back onto the spent liner for collection in the liner waste roll.
Regarding Label or Adhesive Component Inspections we utilize standard vision or barcode reader hardware. Each application is unique and must be assessed to confirm the limits and abilities of inspection.
Please contact Nautilus Systems, Inc. for further information regarding In-line Inspection and Auto Reject options.